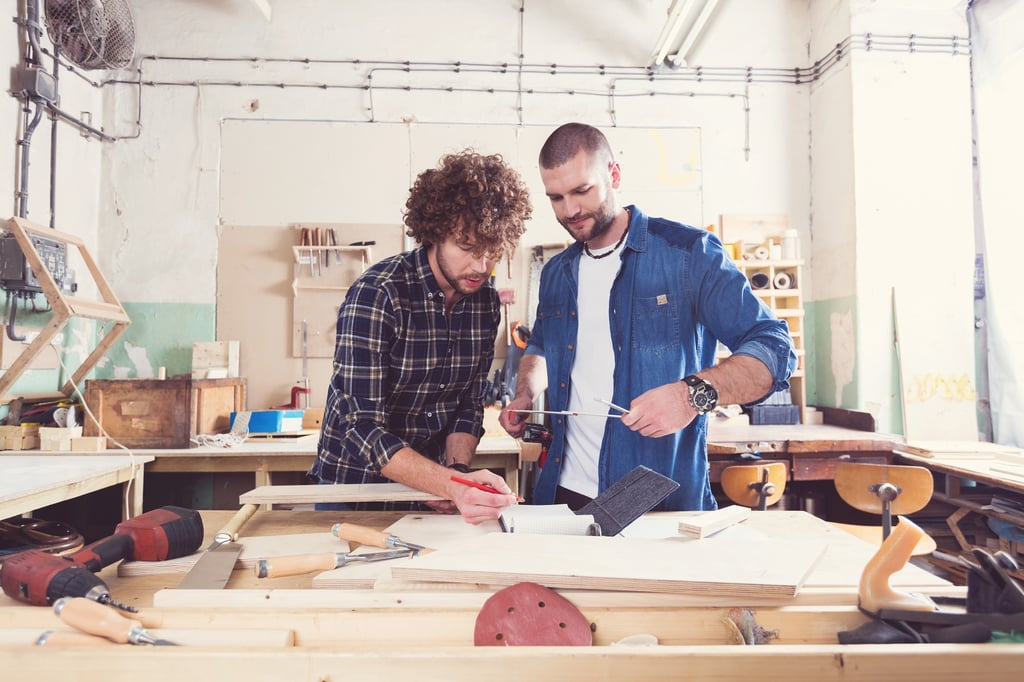
Certify your quality management system with ISO 9001
Overview guide: ISO 9001
Things change; that is a fact. Whilst external factors that are often out of our control may impact our world of work, one thing remains constant: the need for quality management within organisations.
Why ISO 9001 Matters for Businesses Today
In an era of rapid technological evolution, volatile supply chains, and increasing regulatory complexity, organisations must remain agile without compromising on quality. ISO 9001 provides a globally recognised framework for establishing a robust and responsive Quality Management System (QMS) that supports continual improvement and stakeholder trust. Whether you operate in manufacturing, services, or public sector domains, ISO 9001 certification can act as a strategic enabler, aligning internal processes with external expectations.
Organisations that embrace ISO 9001 often report enhanced operational performance, improved customer satisfaction, and greater business resilience - qualities that are particularly vital in today’s dynamic environment.
What is ISO 9001 & Its Strategic Value?
ISO 9001 is an international standard developed to help organisations of all sizes implement a structured, evidence-based approach to managing quality. At its core, it enables you to understand and respond to customer needs, reduce process variability, and consistently meet regulatory obligations. With over a million certified entities worldwide, ISO 9001 is one of the most widely adopted management standards, offering a shared language and structure for quality assurance.
By adopting ISO 9001, organisations not only demonstrate commitment to excellence but also create a foundation for scalability, innovation, and long-term competitiveness.
Key Industry Trends Influencing Quality Management Practices
Several macro-level trends are reshaping how businesses approach quality. The fourth industrial revolution has introduced technologies such as artificial intelligence, additive manufacturing, and robotics, all of which require modern QMS frameworks that are flexible and data-driven. The COVID-19 pandemic further accelerated the need for digital transformation, highlighting the importance of remote audits, virtual collaboration, and supply chain transparency.
In addition, resource scarcity and geopolitical events continue to expose vulnerabilities in global supply chains. In response, quality management systems must now account for resilience and adaptability—not just compliance. ISO 9001’s structure allows organisations to address these complex external challenges while maintaining operational excellence.
Benefits of ISO 9001 Certification for Your Organisation
ISO 9001 certification goes beyond regulatory compliance - it provides strategic and operational benefits that impact every layer of the business. A certified QMS can enhance brand reputation, simplify tender eligibility, and increase the confidence of stakeholders and customers alike.
For many organisations, ISO 9001 serves as a qualification to participate in high-value contracts or supply chain networks. Internally, the implementation of ISO 9001 encourages a culture of accountability, transparency, and continual improvement. It supports decision-making through process-driven data and improves risk management by embedding controls across all critical functions.
When certification is delivered by a globally respected body like LRQA, it signals a deeper commitment to quality, sustainability, and operational integrity.
What Are the Core ISO 9001 Requirements?
Successfully implementing ISO 9001 involves aligning your organisational context, leadership, and planning with the standard’s key clauses. Here’s a summary of what to expect:
- Define Your Organisational Context
The ISO 9001 framework starts by asking organisations to assess their internal and external environment - including cultural, regulatory, and strategic factors. This ensures that the QMS is tailored to your specific operating conditions and business goals. Tools such as SWOT or PESTEL analysis can support this process and help identify relevant quality objectives and risks.
- Demonstrate Leadership and Engagement
Senior leaders must take ownership of the QMS, not just delegate its execution. ISO 9001 requires top management to define a clear quality policy, set measurable objectives, and engage employees across all levels. Auditors will expect to see evidence of leadership involvement in both policy setting and quality performance reviews.
- Address Risks and Opportunities Proactively
Planning for risks is a fundamental aspect of ISO 9001. The standard encourages organisations to anticipate issues that may affect quality outcomes - whether these are process inefficiencies, supply chain risks, or compliance breaches. Equally important is recognising opportunities for optimisation, innovation, or service enhancement.
- Manage Quality Across the Supply Chain
Organisations are also expected to extend their quality management principles across outsourced operations and procurement processes. This means evaluating suppliers, setting clear requirements, and monitoring contract fulfilment with the same rigour applied internally.
- Drive Continuous Improvement
The final component of ISO 9001 focuses on performance evaluation and improvement. Certification requires evidence that you are systematically analysing data, conducting internal audits, and taking corrective actions where necessary. Improvement can be reactive (through root cause analysis) or proactive (through innovation or strategic planning).
- Integrating ISO 9001 with Other Standards
ISO 9001 is built on the Annex SL framework, which provides a consistent structure across modern ISO standards. This makes it easier to implement multiple standards - such as ISO 14001 for environmental management or ISO 27001 for information security - within a single, integrated system.
An integrated management system (IMS) can significantly reduce duplication of effort, improve cross-functional visibility, and align various compliance objectives with overall business strategy. LRQA strongly recommends this approach for organisations looking to scale quality management across multiple domains.
The ISO 9001 Certification Process with LRQA
Working with LRQA gives you access to experienced auditors who understand your sector and tailor the certification journey to your operational maturity.
- Stage 1 – Document Review:
The process begins with an evaluation of your QMS documentation. This stage is often conducted remotely and ensures that your processes are aligned with ISO requirements. - Stage 2 – Implementation Audit:
Your auditor will assess whether the QMS has been effectively implemented and is delivering the intended outcomes. This stage may be on-site or remote, depending on your preference. - Certification Awarded:
Once compliance is confirmed, LRQA issues your ISO 9001 certificate - validating your commitment to global best practices in quality management.
Our approach combines technical rigour with flexible delivery models, including remote audits that reduce travel costs and environmental impact while maintaining full accreditation integrity.
Why Organisations Choose LRQA for ISO 9001 Certification
LRQA is a globally recognised assurance provider with a legacy of delivering high-quality certification services across over 160 countries. We are proud to hold the first UKAS-accredited ISO 9001 certificate ever issued, demonstrating our long-standing leadership in this space.
What sets LRQA apart is our ability to combine sector expertise with a forward-thinking mindset. We don’t just audit - we partner with clients to understand their risk landscape, support their goals, and offer insights that drive measurable improvement.
Whether you are pursuing your first certification or seeking to evolve your existing QMS, LRQA offers the credibility, experience, and global footprint needed to help you succeed.
Download the Full ISO 9001 Guide
If you’re looking to upskill your team or build internal capability, explore our ISO 9001 training courses designed to equip professionals with the knowledge to implement and maintain a compliant QMS.